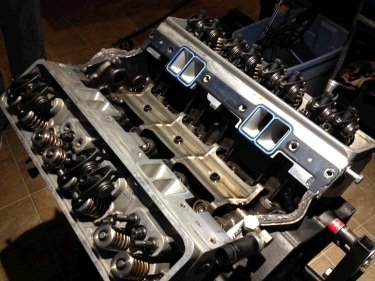
Tear-down shows a clean intake manifold
|
|
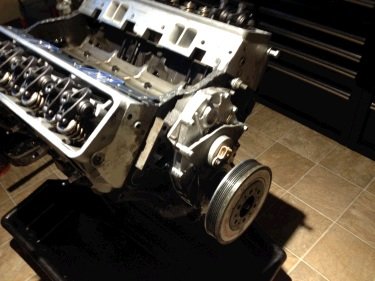
Brian has great success with the EFI Connection 24x system.
|
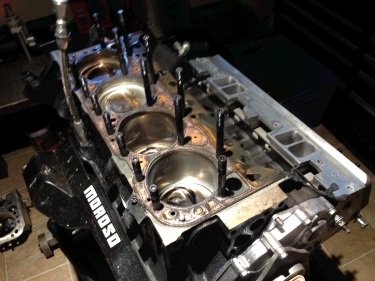
This is a blower motor so Brian used Cometic MLS head gaskets.
He coated them with copper spray which did not seem to hurt a thing.
|
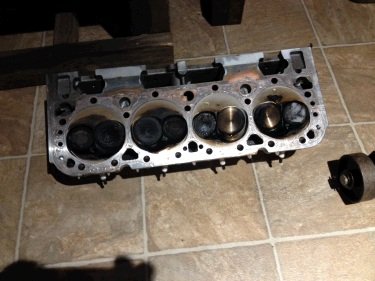
We are looking for evidence of oil consumption. The motor ran
great and made good power but used oil.
|
This is a very well made motor. Good
design. Good machining. Good assembly.
|
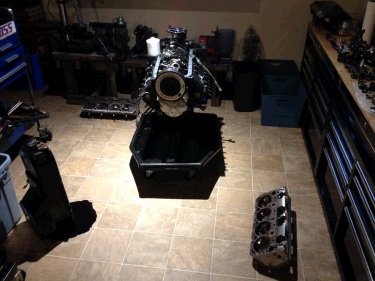
|
|
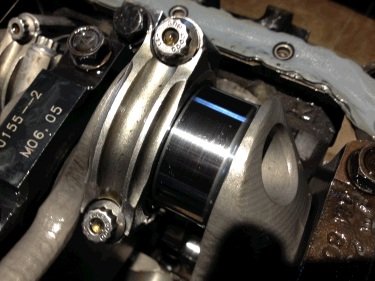
1st rod removed. The Callies crankshaft looks brand new.
|
|
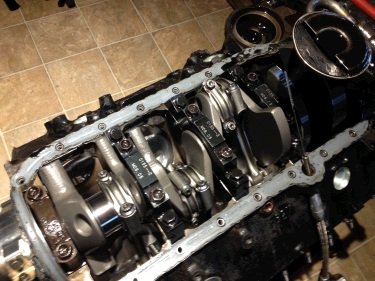
Eagle splayed main caps in the 3 center positions.
|
|
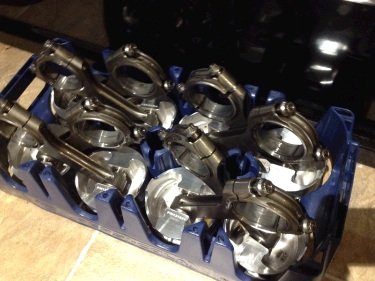
All rods and pistons are in very good shape.
|
|
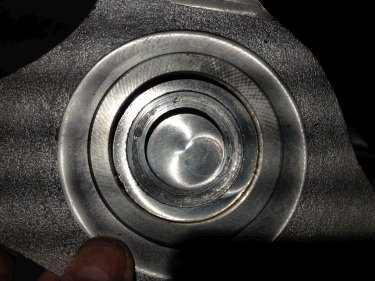
Just a note about the cam pin. When installing the EFI connection cam
sensor, it needs to be shortened a bit.
|
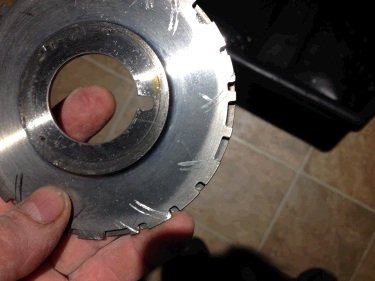
I had the same timing chain rub marks on a recent customer's motor.
|
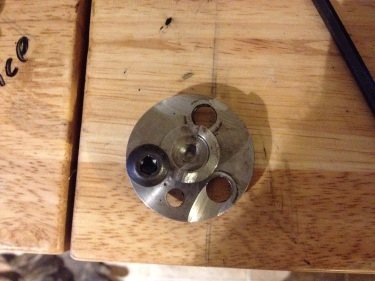
Could not get 2 of 3 cam bolts off. I ended up grinding
the heads of the bolts off.
|
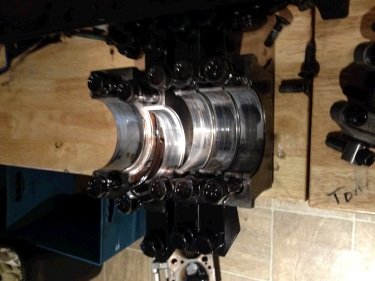
This is a photo of the main bearings. Brian used stock main
bearings and they seemed to work quite well.
|
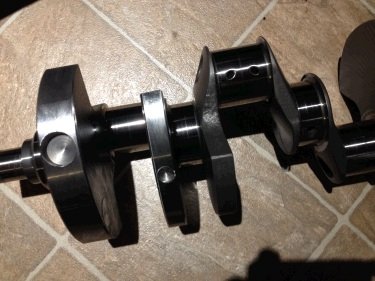
|
|
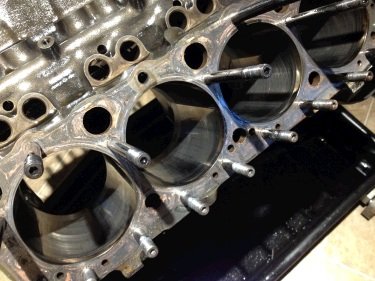
Right now the conclusion is that this shiny area of the cylinder
walls is from fuel wash.
|
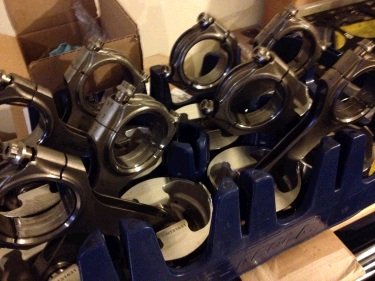
Another photo of rods and rod bearings.
|
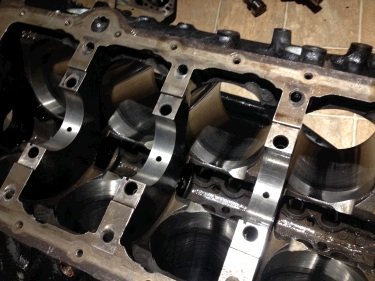
Fuel wash?
|
Next: Heads and
block go to the machine shop.
Valve springs will be checked and re-used if good. Heads will be
cleaned and receive new valve stem seals. Block will be
honed. ARP/Milodon studs will be added to mains and align hone
if needed.
|
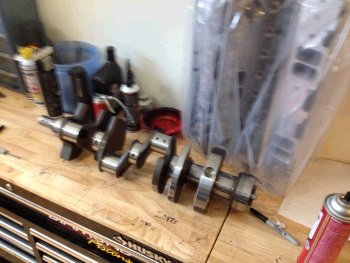
Callies crank rod journals at 2.0990" and Mains at 2.4480"
|
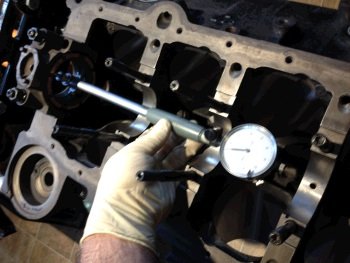
Clearance at .003" using standard size Clevite H
|
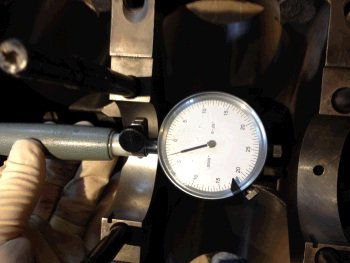
|
|
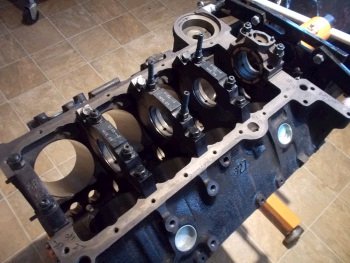
.0027"/.0028"/.0025"/.0028"/.0030"
(1,2,3,4,5)
|
|
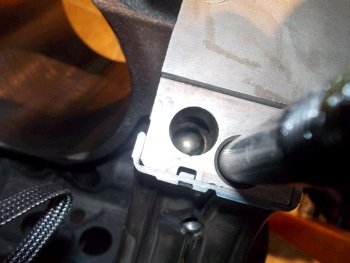
Photo verification that the oil galley plug is installed.
|
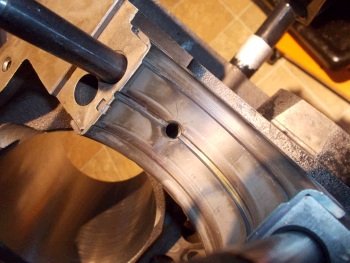
I widened the oil hole in the block slightly to align with the Clevite
H bearing.
|
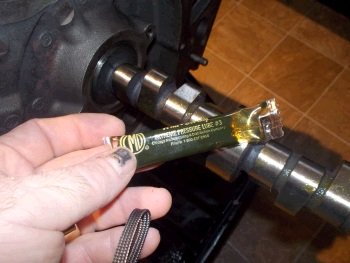
CMD #3 lube on cam lobes.
|
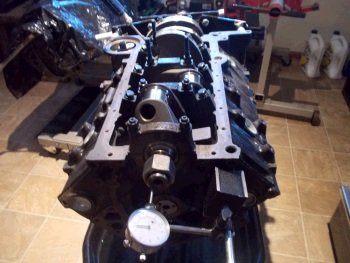
Crank installed and thrust at .008"
|
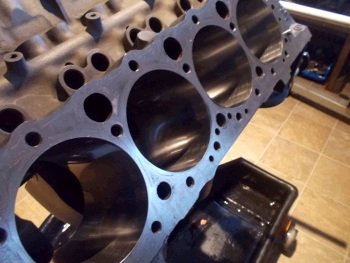
Bores thoroughly cleaned.
|
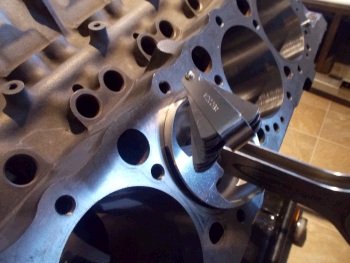
All pistons checked to be .006" piston to bore clearance.
|
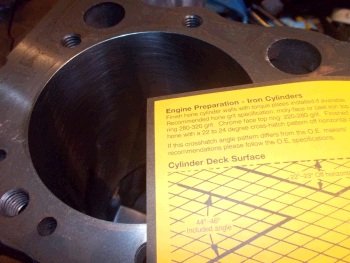
The block was honed to Total Seals spec.
|
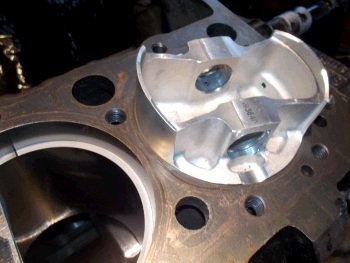
Ring filing. This is my 4.035" piston used as squaring
tool.
|
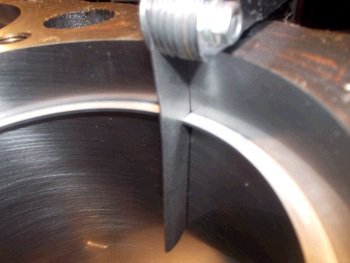
Top ring at .030", 2nd ring at .025"
|
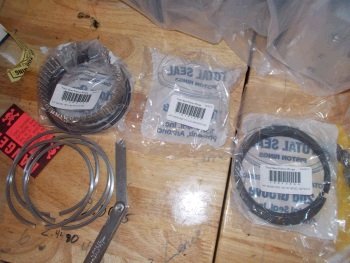
Total seal gapless top ring set.
|
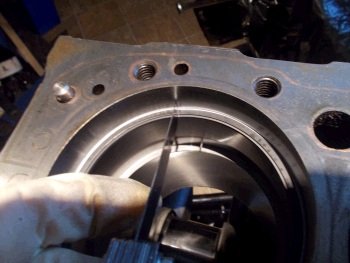
I gapped the "gapless" rings too to .030"
|
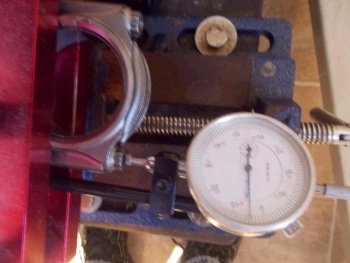
Rod bearing clearance check. Rod bolt at .005"
stretch.
|
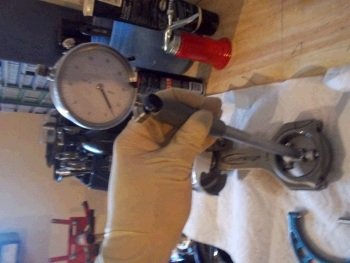
Standard size Clevite HN bearings, (.0022")
|
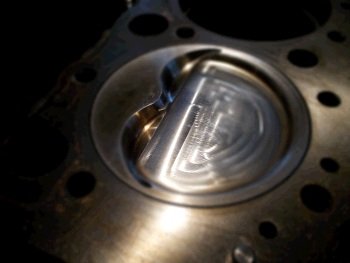
#1 piston in the hole.
|
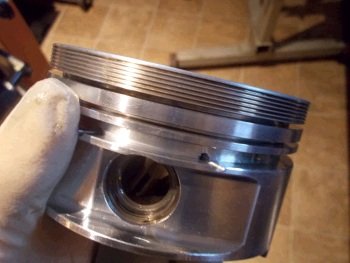
I made sure to clean the pistons, especially in the ring groves.
|
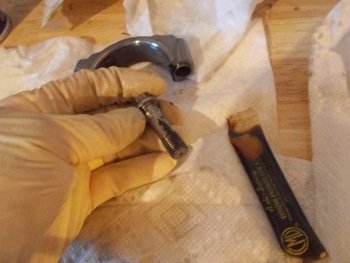
Also re-greased the rod bolts.
|
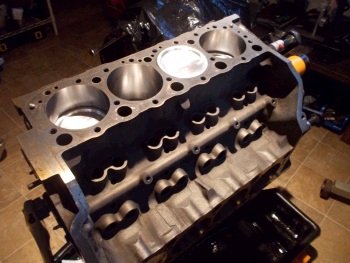
All 8 pistons installed.
|
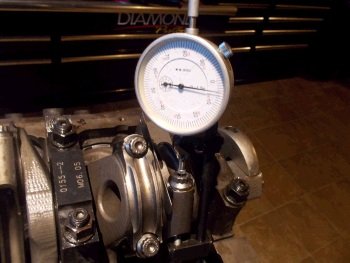
Torquing rod bolts, (75ft-lb)(.005")
|
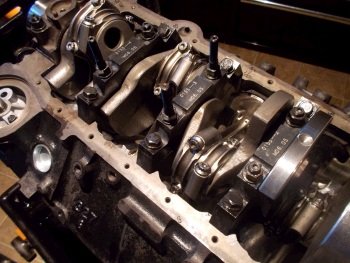
Rod side clearance is .020"
|
|
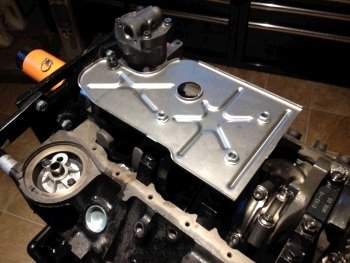
Fitting up a stock windage tray.
|
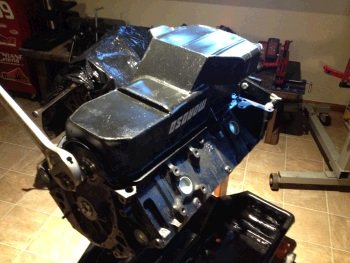
I bent the sides of the windage tray in order for the oil pan to
clear.
|
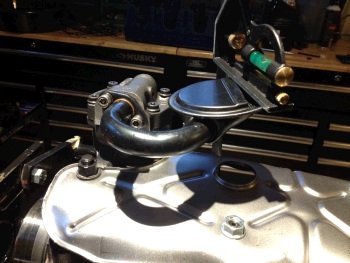
Milodon 10552 high pressure oil pump. The pickup had to be
slightly messaged to fit in the Moroso oil pan.
|
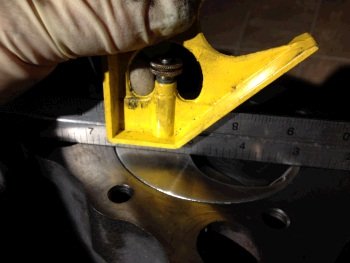
Piston is 0.000" in/out of the hole.
|
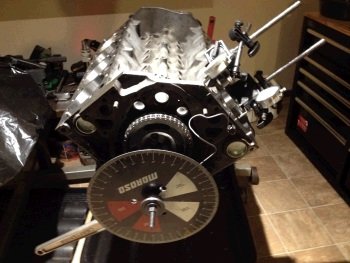
Cam degree check. ICL at 109deg right on with the cam card.
|
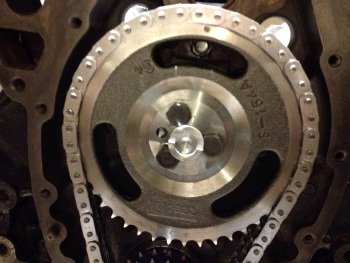
I was able to ditch the EFI connection cam bolts and use stock cam
bolts.
|
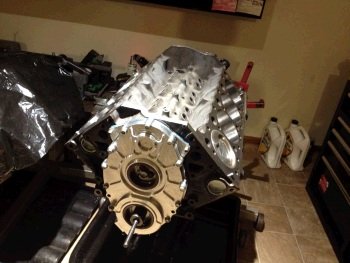
|
|
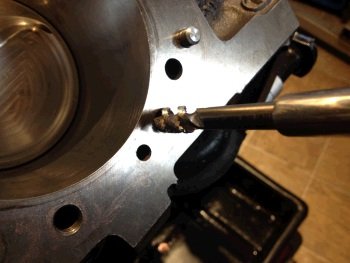
I have a head bolt thread cleaning tool and put it to good use.
|
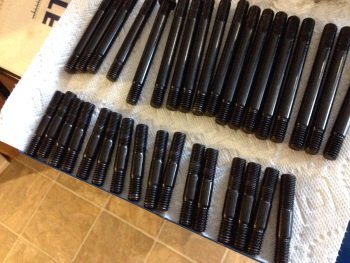
Head studs cleaned with soap and water.
|
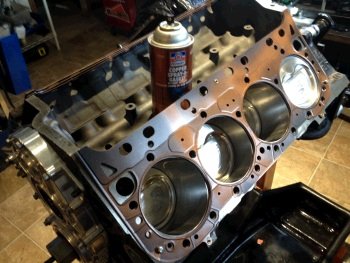
Cometic says not to use copper spray but....
|
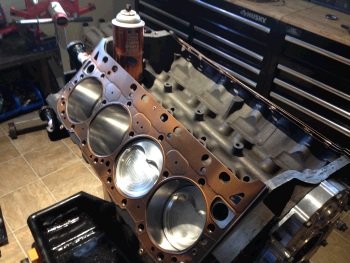
....the Jeg's Engine Master Lennart Bergqvist uses this technique.
I sprayed in-between all three layers.
|
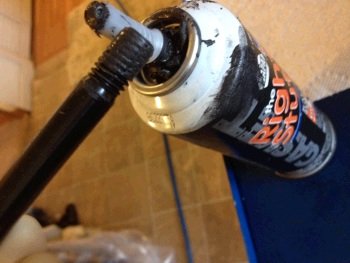
My method to seal the head studs is to use Right Stuff RTV
|
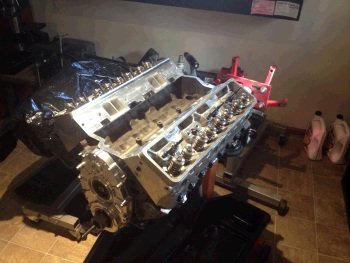
Heads on and torqued.
|
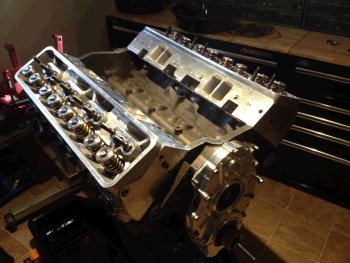
|
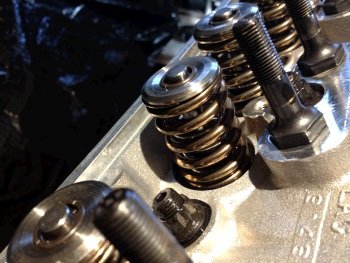
These are very good looking valve springs. I took a photo just
for my enjoyment.
|
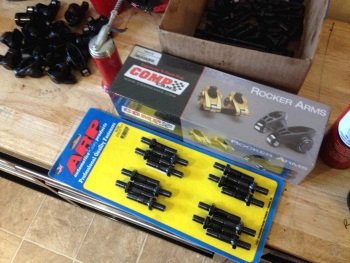
Swapping over to 7/16" rocker studs from 3/8"
|
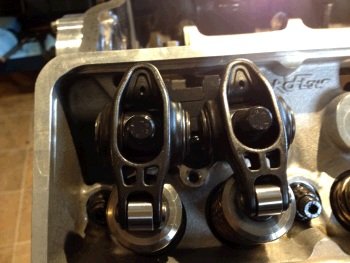
These are non self aligning rockers. We are using Isky
adjustable pushrod guide plates.
|
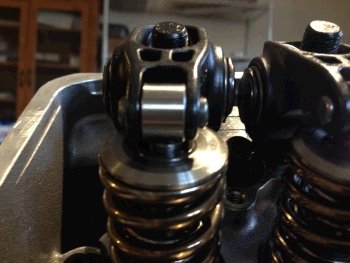
|
|
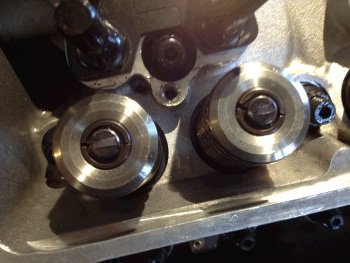
|
|
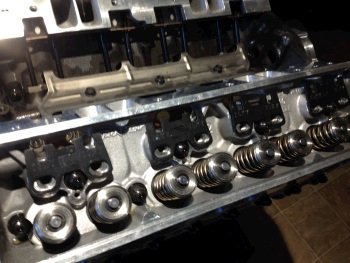
Here is a good view of the ISKY guide plates.
|
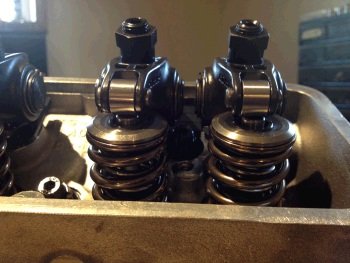
It may not look like it but the rocker tips are well centered.
|
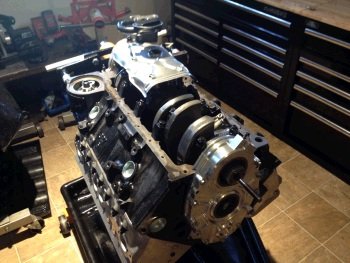
One last view of the bottom end.
|
|
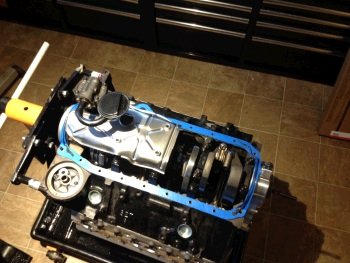
RTV on the oil pan gasket at just the front and rear ends.
|
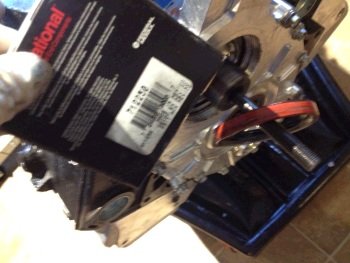
Old crank seal hanging and new in the box.
|
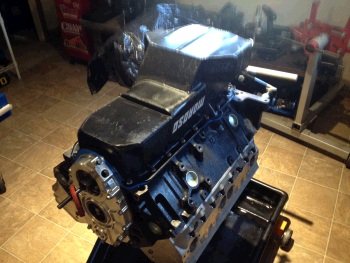
Oil pan on.
|
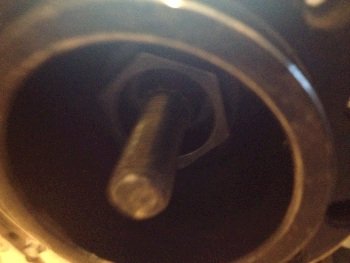
Photo of the nifty Callies crank stud.
|
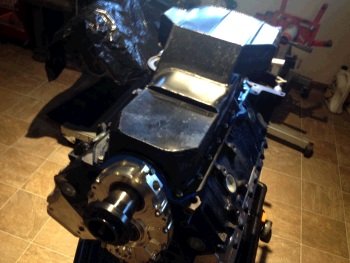
|
|
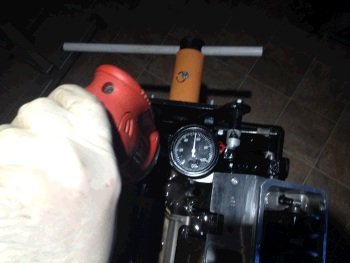
Oil pressure check. All good.
|
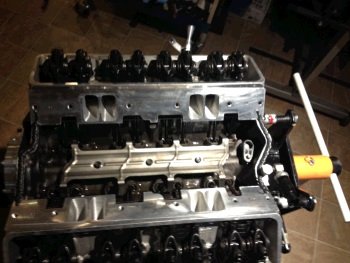
Last view of the intake valley.
|
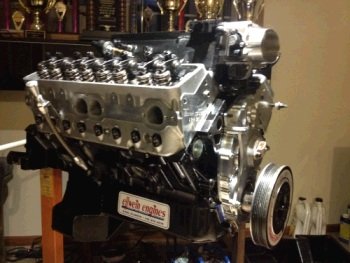
Intake manifold on and posing for photos.
|
|