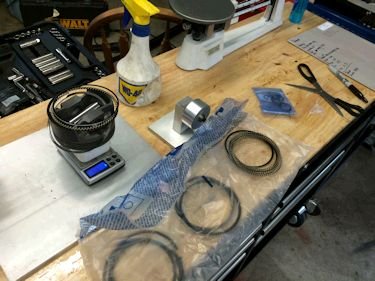
Mahle 383 pistons for 6" rod.
|
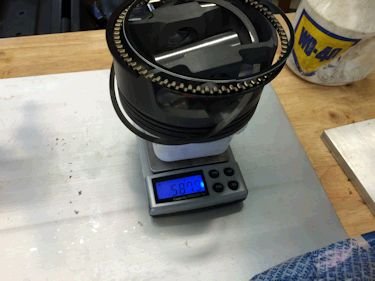
Total weight with pin and rings = 588 g
|
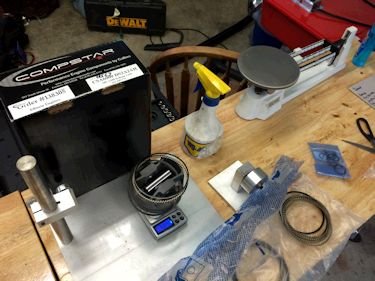
Compstar 6" rods at 449/174g
|
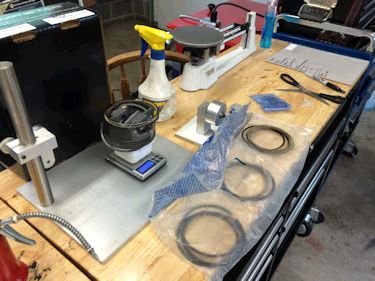
King bearings @ 38g gives 1740g bob-weight
|
|
|
|
Milodon center 3 main
caps and ARP/Milodon main studs. Block headed for main cap shop.
|
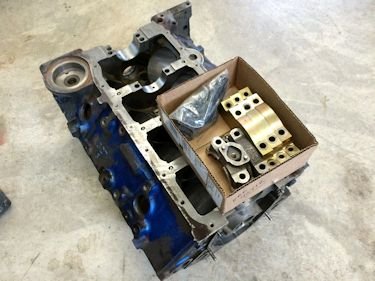
Many weeks later the block is back from the main cap shop and the
bore/hone/deck shop, (Advanced Automotive Machine in Waldorf
Maryland).
|
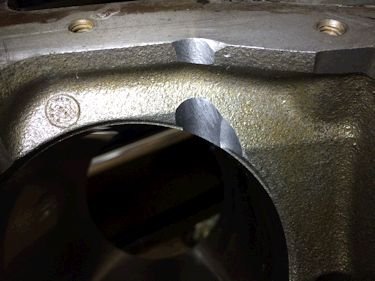
Here is a typical view of the area I clearance for the crank/rod
stroke.
|
|
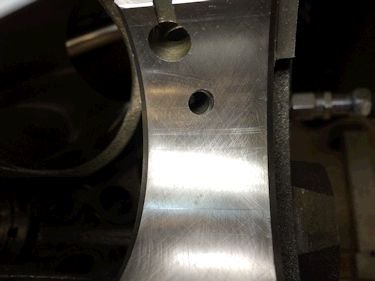
Here is the main cap oil feed hole that is slightly massaged to allow
the oil to flow into the King main bearing.
|
|
|
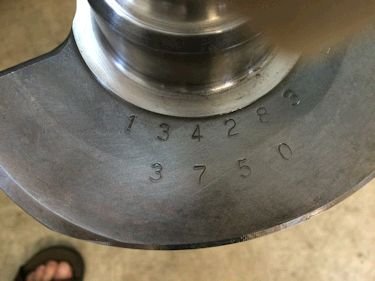
The Callies crankshaft.
|
|
|
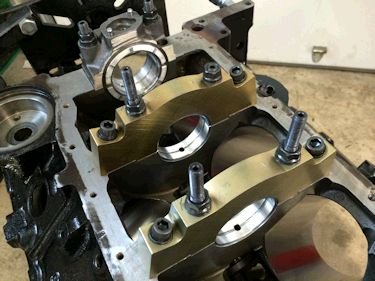
Mains are a bit tight after the cap machining process. With
standard sized bearings they center 3 are at .0010" (close to
stock size). "X" size are on order and they should
bring the mains out to .0020"
|
|
|
|
|
|
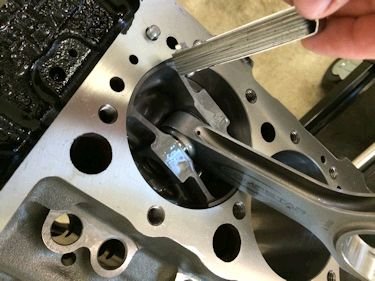
Pistons to bore clearance is .0040".
|
|
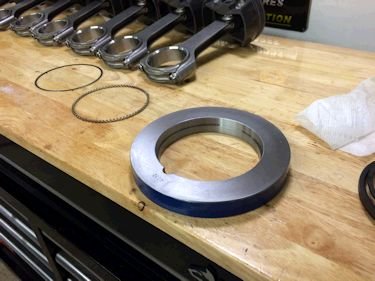
Ready for ring gap
filing.
|
|
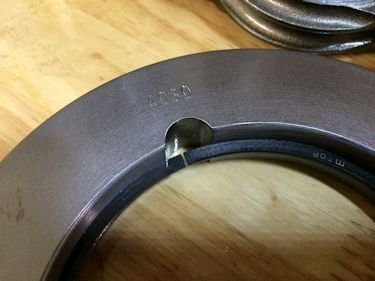
Top and 2nd ring at .020"
|
|
|
|
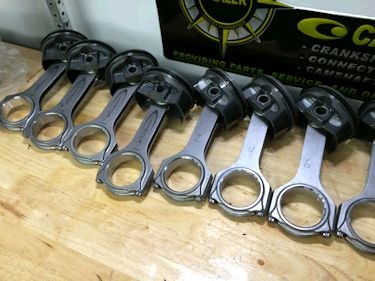
Rod bearing clearance at .0023 to
.0024" with King HN bearings (mix of standard and .001")
|
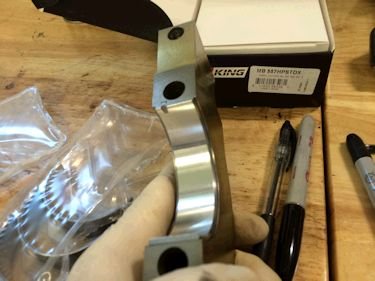
Ok, now back to the main caps and main bearing clearance.
The .001" oversize set arrived. I spoke with the machine
shop that does the main cap installation and they said that they shoot
for the low side of the spec. That sounds reasonable. The
"x" bearing set will bring me to .002" which is NASCAR
tight and good for keeping rod bearing oil pressure up.
|
|
|
|
|
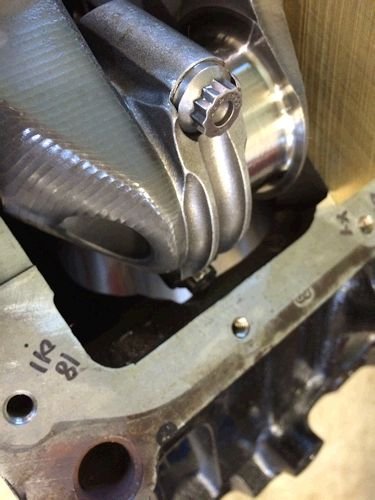
Now installing a few choice
rod/piston sets to make sure the block has been clearanced well
enough. Poor focus on this photo, sorry. I have learned
over the last few engine builds that I should not install the cam
bearings until a full mock-up of crank/rods/pistons has
happened. If I need to grind more on the block then I'll need to
remove the cam bearings if they were installed in order to get all the
dirt out.
|
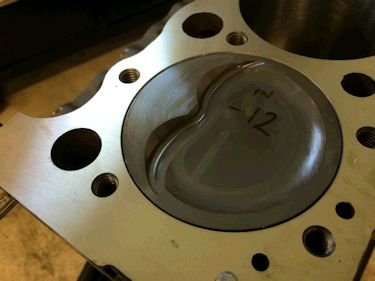
Piston is 0.012" in the hole
|
|
|
|
|
All rods/pistons installed and all clear
the block (almost) well-enough. I spent some time giving a bit
more clearance and then re-washing the block.
|
|
|
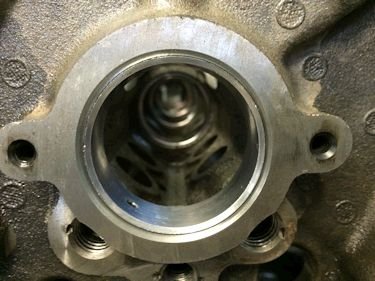
Dura-Bond cam bearings installed.
|
|
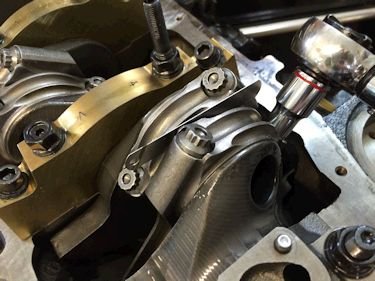
Rod bolts at 75ft-lb
|
|
|
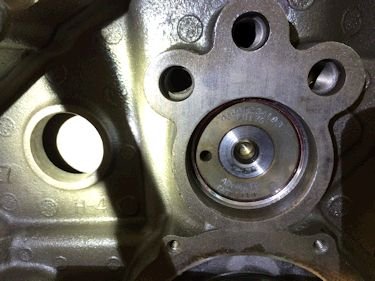
Advanced Induction camshaft
|
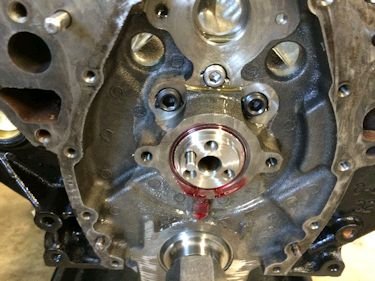
Threaded oil galleys
|
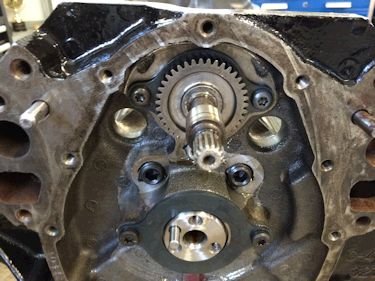
Cloyes timing set with new oil pump drive sprocket.
|
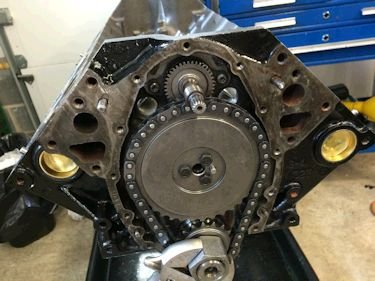
Timing set installed at "0"
|
|
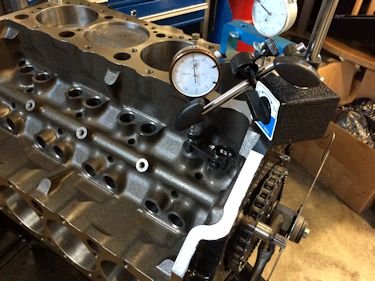
Intake centerline at 105.5 deg. (as per cam card)
|
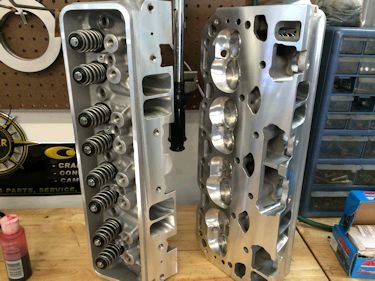
Ai (Advanced Induction) CNC ported heads.
|
|
|
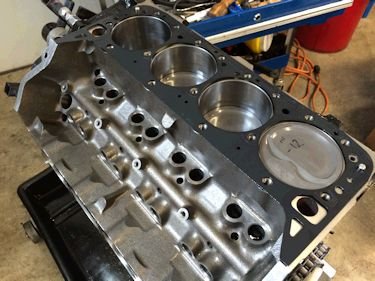
0.026" thick gasket = 0.038" quench
|
|
|
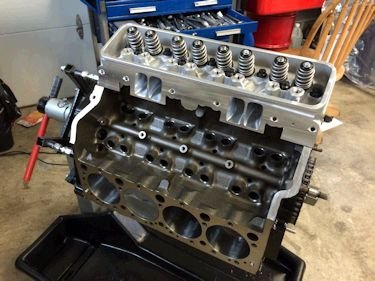
Left side head torqued on with ARP
head bolts.
|
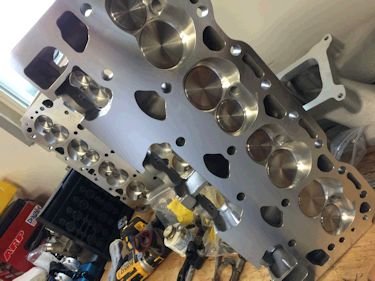
Right side head.
|
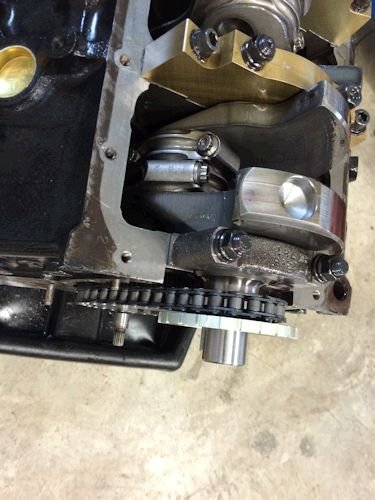
Now the EFI Connection 24x reluctor
|
|
|
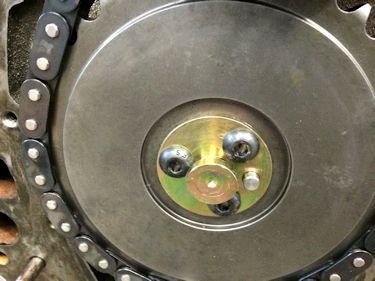
Cam reluctor
|
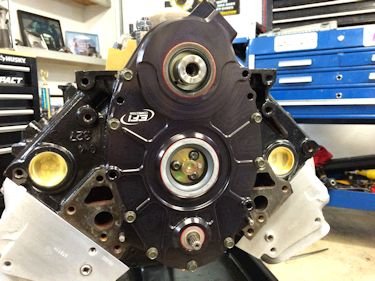
Billet aluminum timing cover
|
|
|
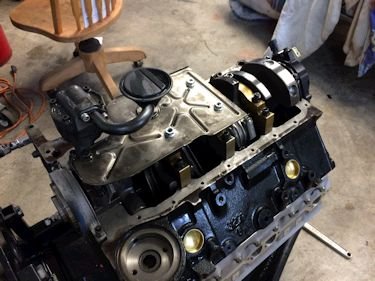
Melling 10552 oil pump.
|
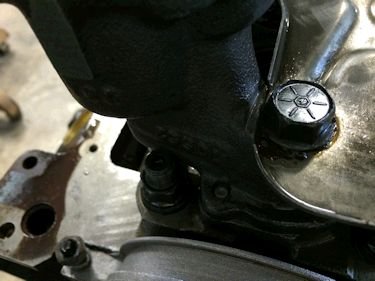
the pump touches the rear main cap stud.
|
|
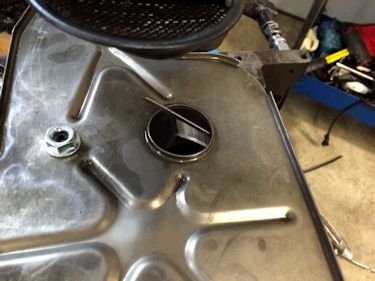
Dip stick fits mostly ok after trimming the tube shorter.
|
|
|
|
|
|
|
|
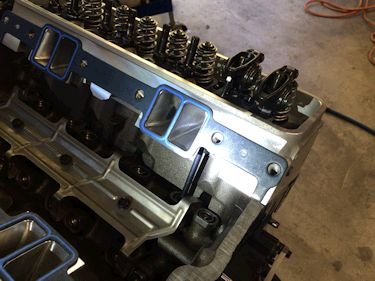
Comp roller rockers test fitted. Pushrod length usually ends
up being 7.2" Here is the mockup.
|
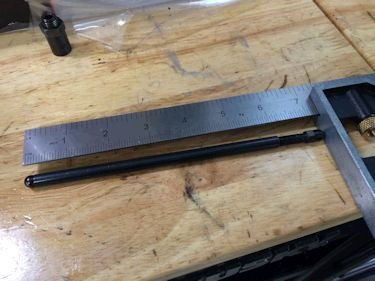
Manley pushrods ordered. MAN-25733-16, Chromoly Steel, Heat-Treated, 5/16 in. Diameter, 7.200 in.
Length
|
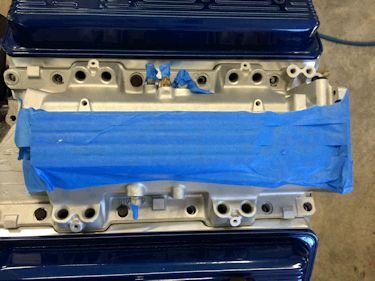
Ai ported LT1 intake manifold test fit. I usually have to
widen the bolt holes to 9/16" wide.
|
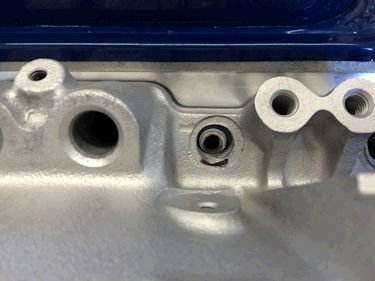
With a little fine tuning with the drill bit for some holes.
|
A note on intake manifold thread
sealant. The bolts thread into the engine oil crankcase lifter
valley and are not under vacuum or pressure. So why is there
thread sealant on the bolt threads? The best reason is to
minimize metal or other junk that can move from the threads and into
the intake valley. The thread sealant might catch potential
metal shaving that can be made during the installation process.
|

Manley 5/16" pushrods, (7.200")
|
|
|
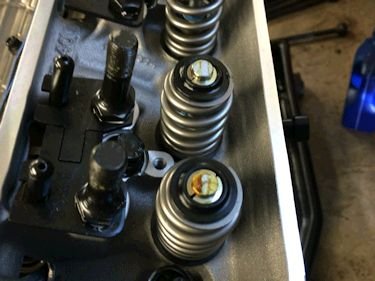
ISKY adjustable guides.
|
|
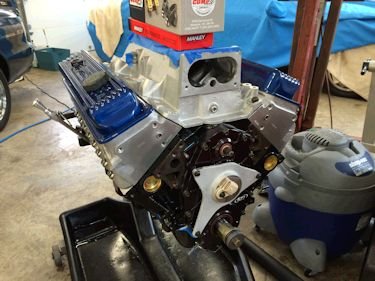
Still to-do: widen a few intake manifold bolt holes and spin the oil
pump and test for pressure and lifter oil to the rockers.
|
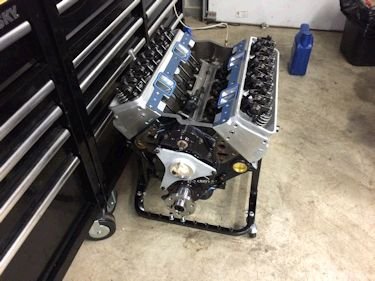
Rear cam plug installed. (it's easier to install the rear plugs
with the engine removed from the work stand).
|
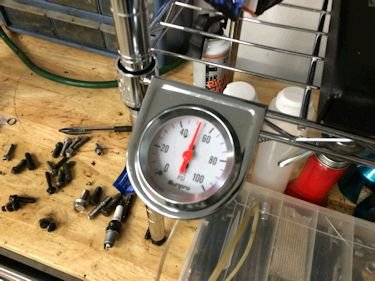
Good oil pressure with a low speed battery powered drill.
|
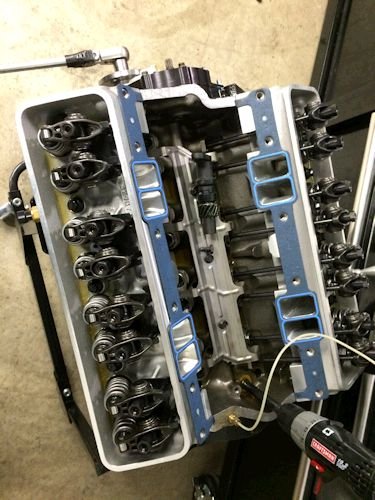
All pushrods brought oil up to the rockers.
|
|
|
|
|
|