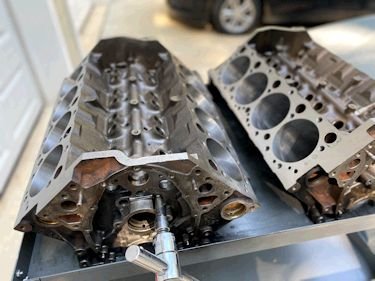
Tapping the oil gallies for threaded plugs.
|
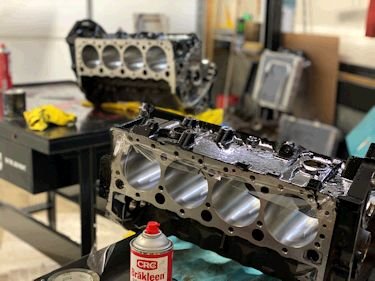
Doing two blocks at one time to economize paint wastage. |
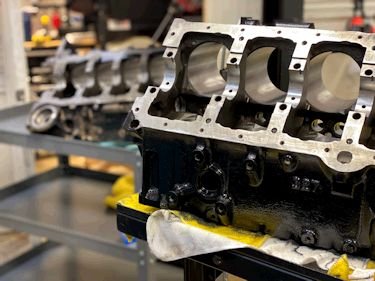
Here you can see the block with the core plugs installed.
That means it received a 1/2 fill of epoxy in the water
jacket. This can still be used on the street but the oil
cooling system has to be it tip top shaped.
|
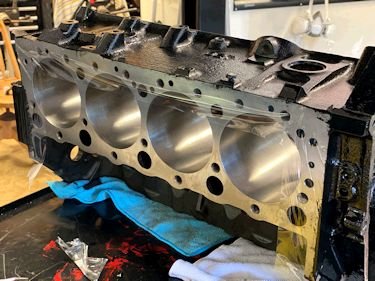
POR-15 engine paint. |
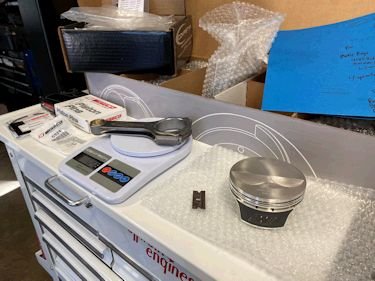
Here I'm re-doing the balance weight. I decided to go with
a Wiseco dedicated nitrous flat top piston. Bob-weight is now
1693 grams
|
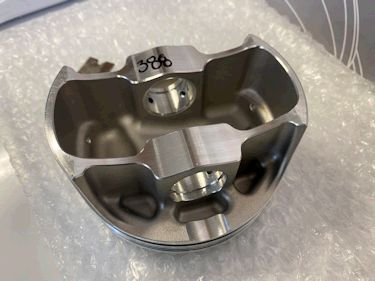
This is the Wiseco #K0001X4
1.125 CH, 388g. The forging has weight savings built in but
it is touted as still being extra strong for nitrous. |
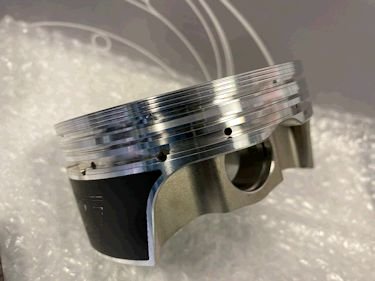
The piston also has lateral gas ports. Also 2618 alloy
aluminum, 1st ring is down .250", -5.7cc valve relief's.
|
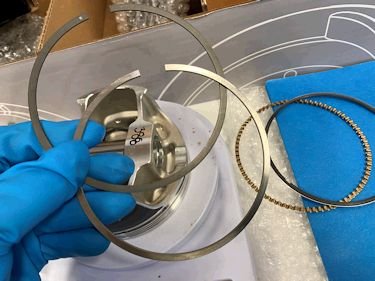
The rings are the Wiseco GFX at 1.2/1.2/3.0mm
The 1st ring is alloy steel and gas nitrided, the 2nd ring is cast
iron with an under-hook face. |
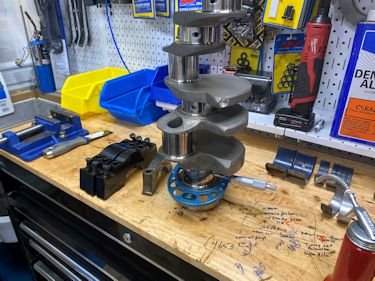
This forged Eagle crankshaft is very good quality for the
money. I have the balance shop polish the main and rod
journals. It was balanced to 1693g bobweight. #5 main
journal being measured here. It is 2.4485"
|
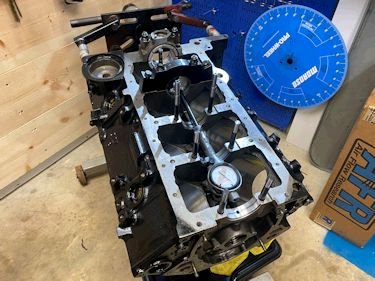
Measuring main bearing clearance. After this I'll set the
crankshaft in and install all rods/pistons (without rings).
This is the "mockup". I will be able to verify
clearance. If more grinding is needed then I'll mark the
areas and tear-down and grind and clean. If no additional
clearance is required I'll still tear it down and do a final
washing of the block. |
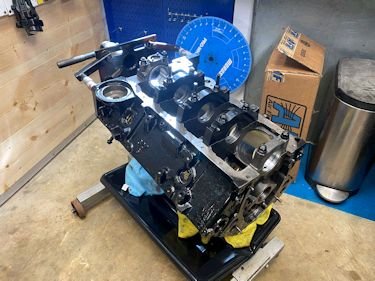
This is a 1/2 filled block and the oil will get warmer than
usual. I have bearing clearance a bit more than usual.
#1=.0027 #2=.0027 #3=.0030 #4=.0027 #5=.0040"
|
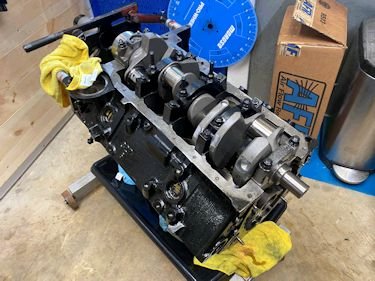
Crank in and it spins nicely with 30w oil, (no assembly lube). |
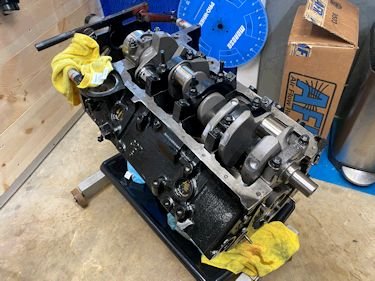
Duplicate photo but I'll leave it here.
|
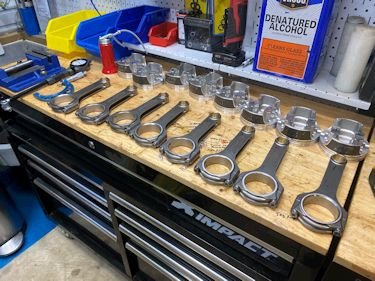
Callies Compstar rods and Wiseco flat top K0001X4 piston. |
|
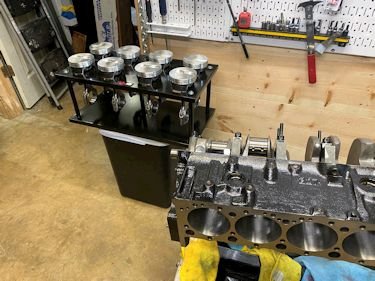
Assembly of rods to pistons. These use a spiro-lock.
They are a pain to install. Rod bearing clearance not
measured yet. I'll do that after the rotating assembly
mock-up. |
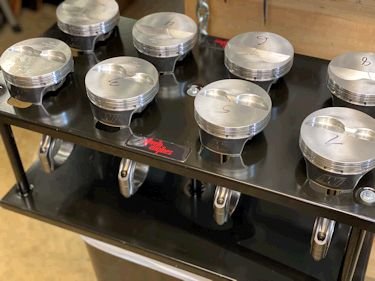
I checked piston to cylinder wall clearance and it is
.004" Recommended .0035" (at least). The block
is filled and so it should have more clearance and so .004" is
good.
|
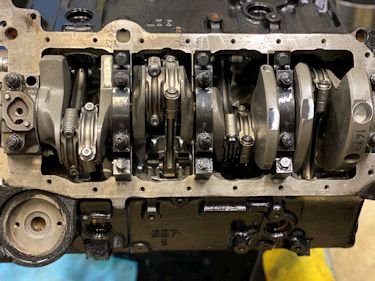
All mocked up. 2 spots need a little more clearance, (marked
in yellow). Nothing hits but it's close at the rod bolt
shoulder with #4 and #6. |
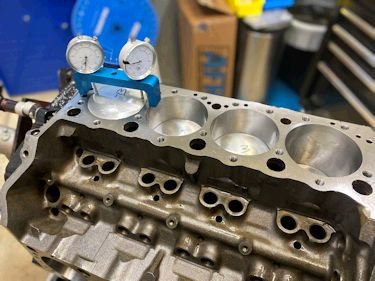
While I'm at it I want to see if the block is decked square.
Very close to perfect.
|
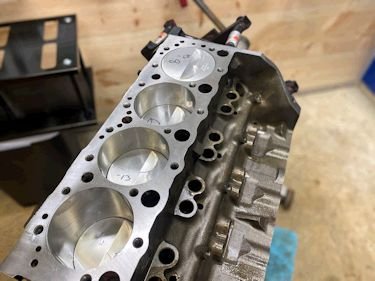
It is 0.013" in the hole at all corners. |
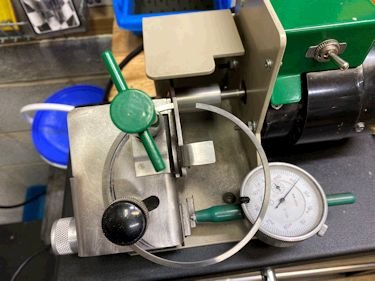
Now it is time to file fit the piston rings. These are
from Wiseco and I do believe they are Hastings brand. Good
quality steel top rings and napier hook style 2nd ring.
|
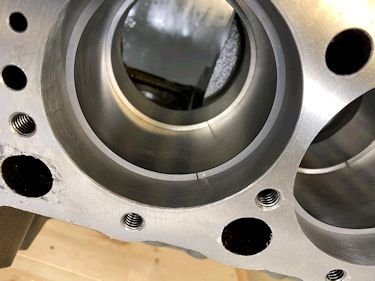
Gapping for nitrous race only. I shot for .028" top
and .029" 2nd ring but "over-shot" and so it ended
up being .029" top and .030" 2nd ring. Throw all
the nitrous at it that your heads will allow. |
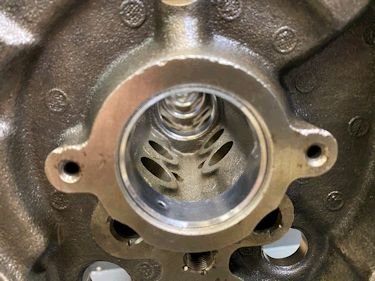
Cam bearings installed.
|
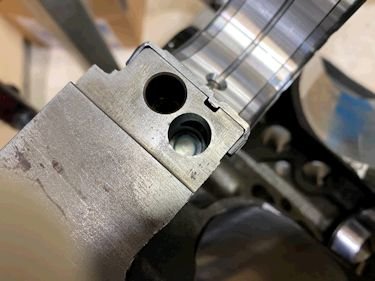
I kept this oil galley plug out until final block
washing. Earlier in the day I did the minor block
clearancing that was needed for rod clearance. Now it's time
for final assembly. |
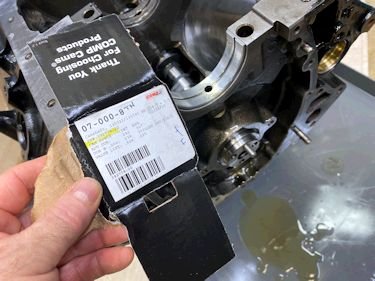
Camshaft from Lloyd Elliott. I like to have the camshaft
installed while I insert the rods/pistons in order to make sure the
rods do not bump the cam.
|
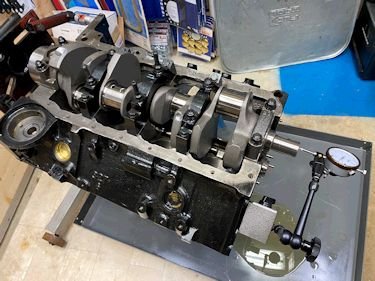
Crankshaft back in and thrust checked at .006" |
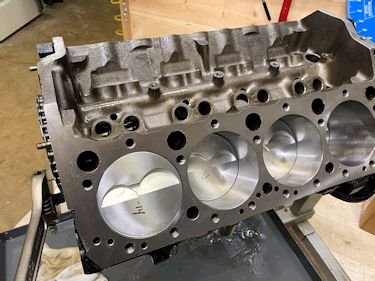
All pistons/rods installed.
|
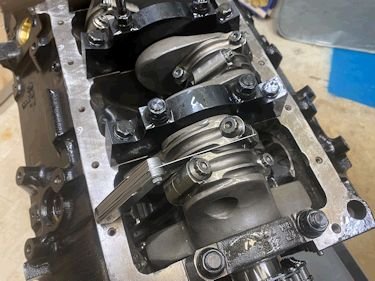
Side clearance is .020" with these Callies rods and the
Eagle crankshaft. |
|
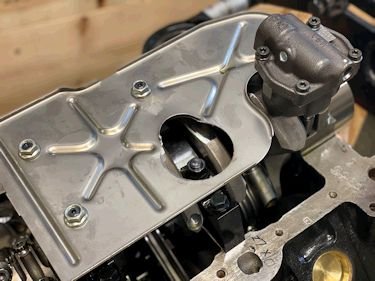
Windage tray dip stick hole enlarged. I try to make sure
there are no metal burrs after doing this. From this photo I
can see one. I guess that is one good reason to take high
resolution photos. |
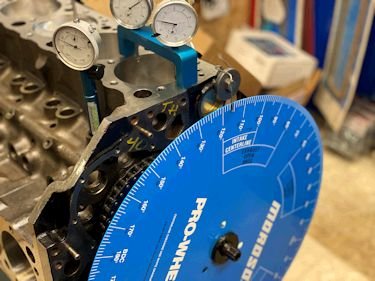
Camshaft degree check. The cam card calls for intake
centerline at 111 deg. I have the Cloyes timing gear at zero.
|
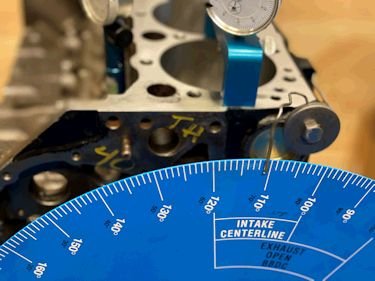
Intake centerline as found---111 deg. Now I can put blue
loctite on the cam bolt threads. |
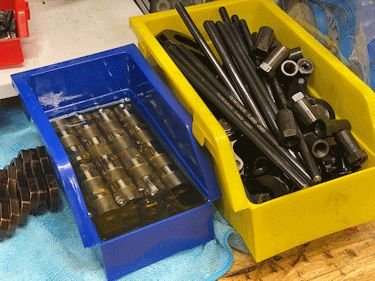
Lifters and pushrods cleaned and soaking.
|
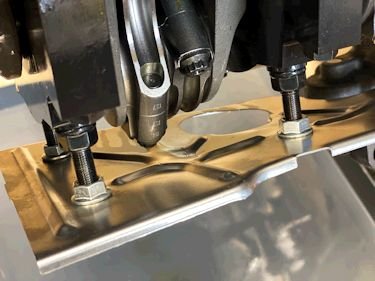
Here is a photo of the windage tray bent slightly so that the
rods do not bump into it. |
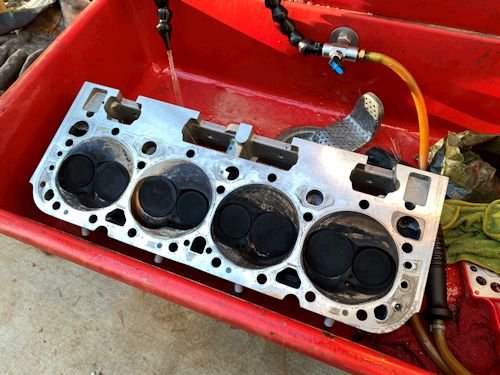
21 degree Trick Flow cylinder heads being cleaned up as much as
I can with a Safety Kleen parts washer. The heads were working
well on Tucker's old combo.
|
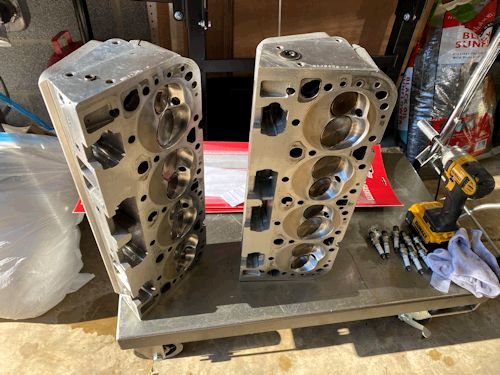
The heads were ported by Lloyd Elliott and as far as I can
tell they are still in great shape. |
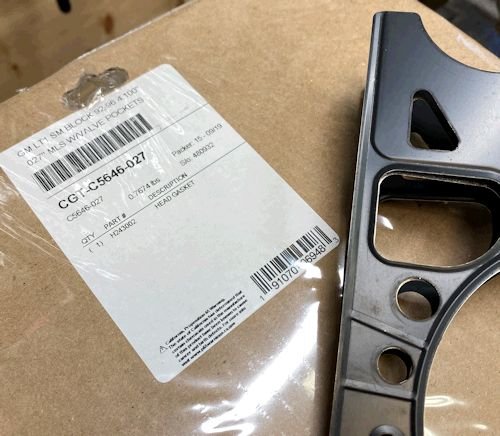
Since the pistons are .013" in the hole then this thinner
MLS head gasket will work well to keep piston to head gap
reasonable. 27 + 13 = .040"
|
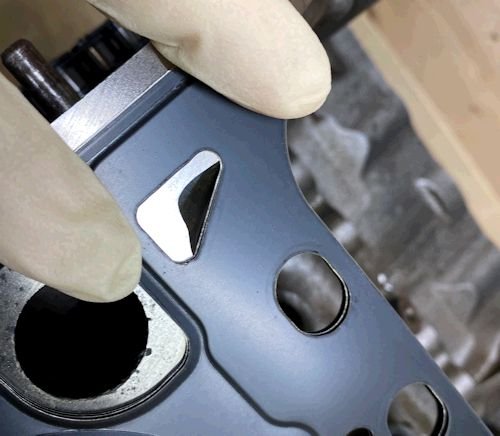
This photo shows were Cometic MLS gasket blocks off the oil
return at the left front corner of the block. Not now
because I grind on the block right here to make room. |
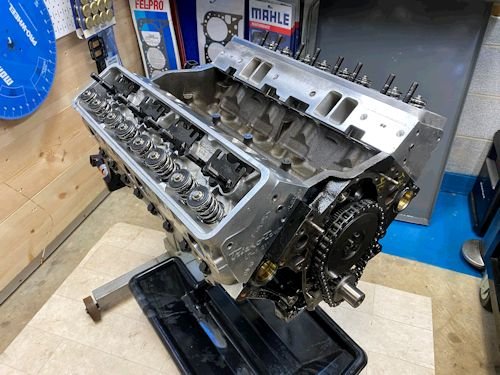
Heads are on with customer supplied ARP head bolts. All
bolts at 70ft-lb
|
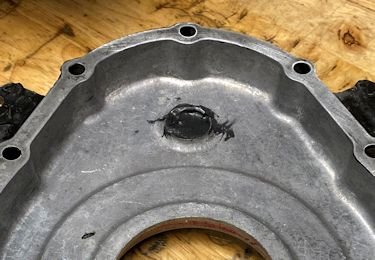
I donated a timing cover and this one has the water pump shaft
hole blocked off with a Kennedy .50c piece. I added more RTV
on the back side for good measure. |
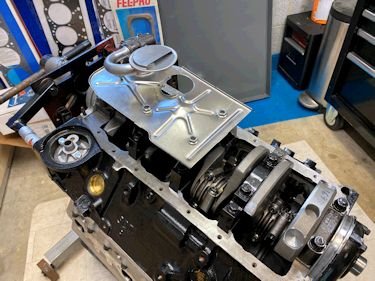
Oil pump pickup pressed in. I'm not a fan of tack welding
this. They can move but they don't fall off.
|
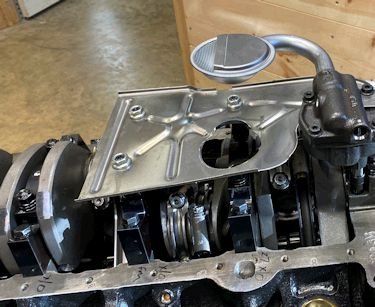 |
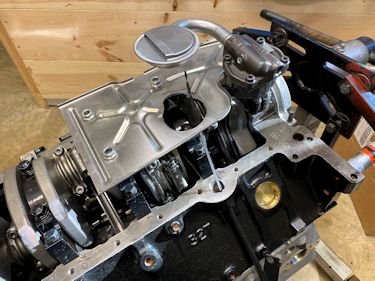
Dip stick test to make sure the stick bends over the wide main
cap without taking a path into the rods.
|
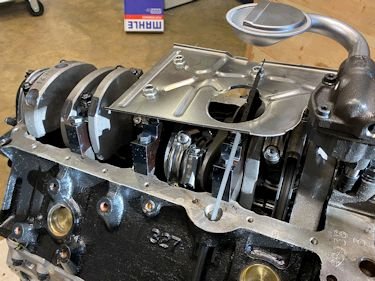 |
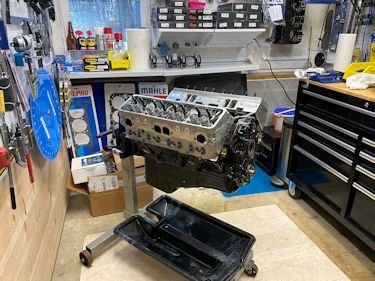
Oil pan on. RTV on the block side of the gasket but not the oil
pan side. That should make for a good seal and also allow me
to remove the oil pan after the engine dyno session. If it
ends up leaking then more RTV!!!
|
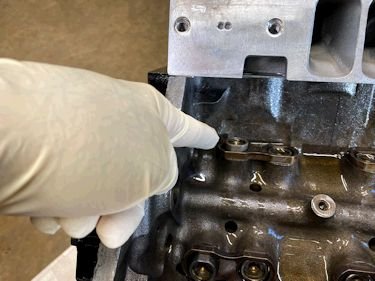
The lifters are re-used from the previous engine and all of
them are in good shape except one had the beginning of a
mushroom. It would not fit in the bore nicely. It fit
but it was a tad tight in the bore. I replaced it with a
nice stock lifter. |
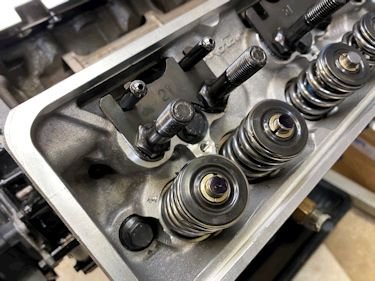
I'm going to learn something here. The old pushrods are
7.400" long and that is not the ideal length that my lifter
length check tool recommends. (7.250)
|
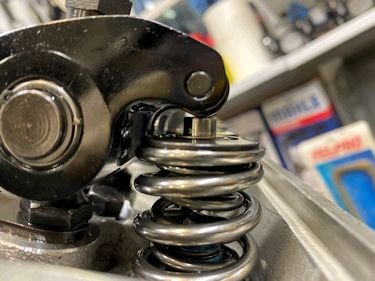
But the 7.400" seems to fit quite well. |
|
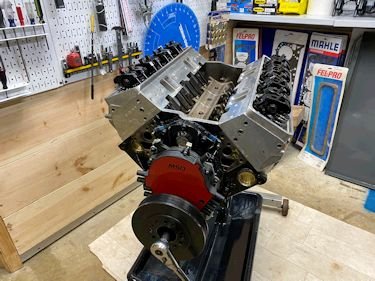
So we shall stay with what was working with the old
combo. I like the Lunati rockers. The 7.400"
pushrods give a very good witness mark. |
|
The opti spark is installed just
temporary for the dyno. The damper is my dyno damper
too. It has timing marks on it which is a big help for the
dyno. Next update will show the engine at the dyno.
(in a week or 2). |
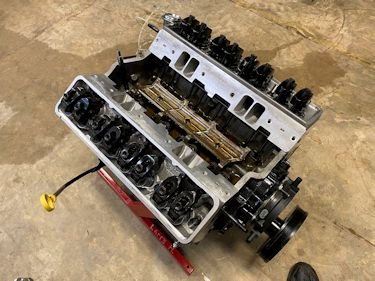
Getting ready for the oil system test. Off camera it did
not work out well. The front oil galley plugs were
accidentally left out. This is the main reason why I do the oil system
test...to catch my mistakes.
|
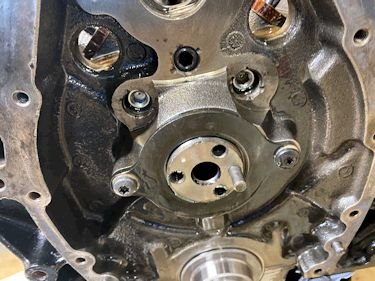
A few hours later I have the cam timing set removed and now I
have installed the oil galley plugs. |
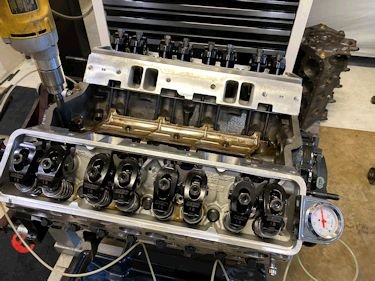
All back together and now the oil test is good.
|
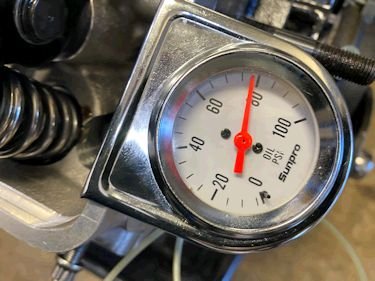
Lots of oil pressure. |
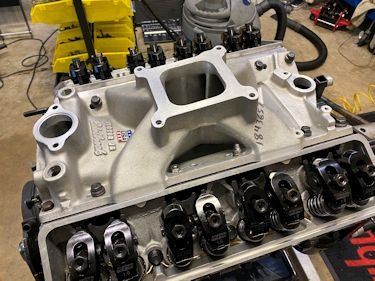
Now getting ready for the engine dyno. Single plane carburetor
manifold.
|
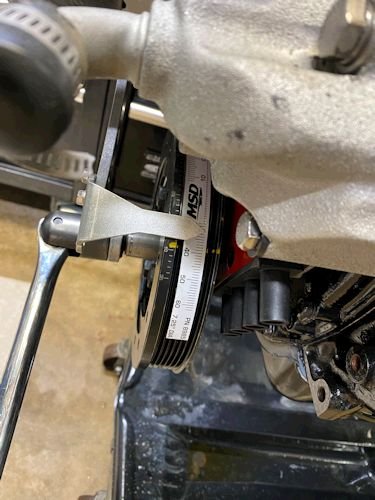
Timing pointer |
v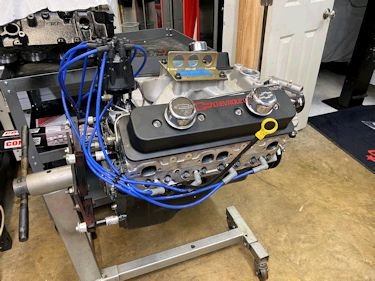
All set and ready for Wednesday
|
|