|
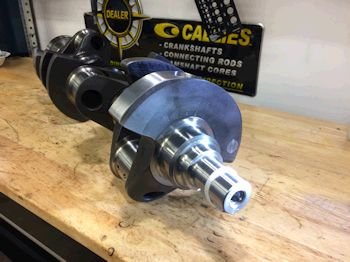
Here is our Callies USA steel Dragonslayer crankshaft. This is
balanced by Callies to 1723g (Neutral).
|
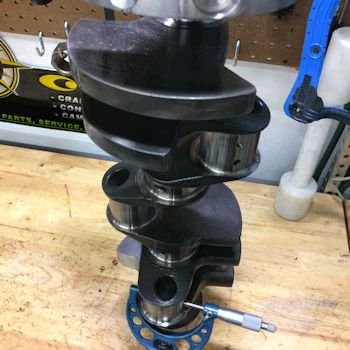
Crank rod journals at 2.0987"
|
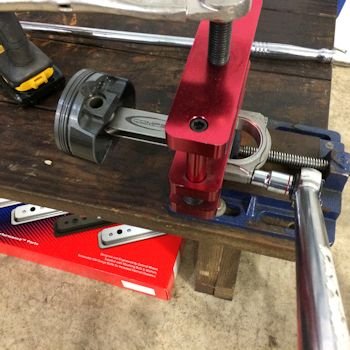
Callies Compstar H-Beam rod bolts torqued to 75ft-lb with King
CR807HPN rod bearings.
|
|
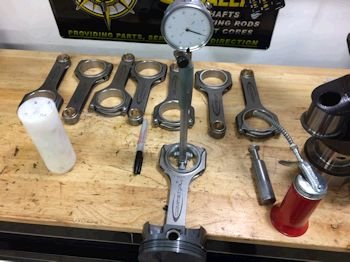
A mix of standard and .001" under give 0.0026" bearings
clearance.
|
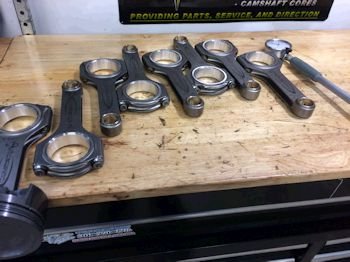
We are using the Mahle D-dish piston with 1mm ring pack. It
it truly the best piston for the $$$.
|
|
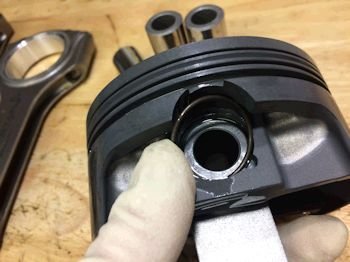
Installing the F1 wire clip is a breeze.
|
|
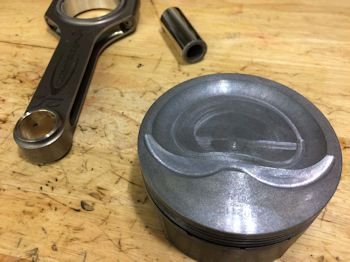
The piston is a -18cc D-dish which will give us 11.07:1 static
compression ratio with the 54cc LE heads.
|
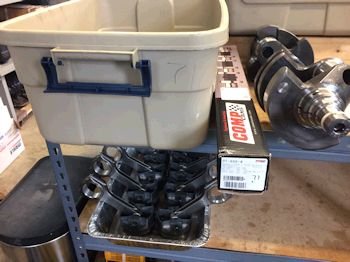
Here I have assembled all the piston/rod sets and measured rod
bearing clearance. All rods are at .0026" bearing
clearance.
|
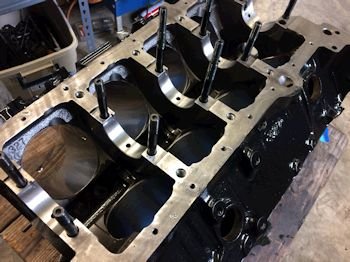
The block is spending some time waiting for the POR15 to
dry. We can do main bearing clearance while we wait.
|
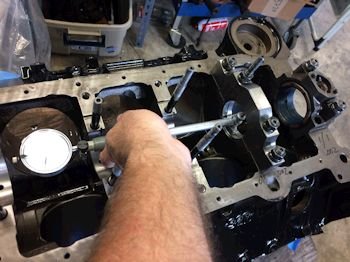
Rear main is at .0020 with a coated set of Clevite MS909-HK,
(.001" under). I had a set of these very expensive bearings
in the drawer and finally found an engine that can use them.
|
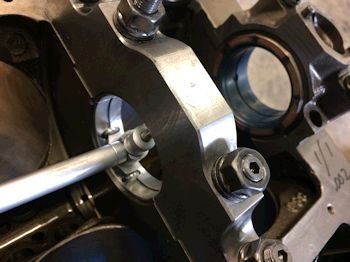
The #2,3,4 mains receive my favorite brand of bearings, the King
MB557HP. Mix of .001 and STD.
|
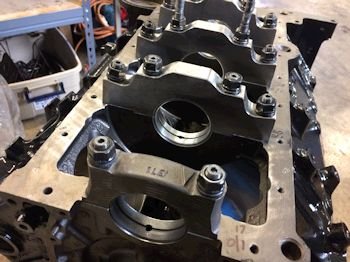
Mains generally at .0020" except for #1 which is at
.0017". #1 has the coated MS9099HK.
|
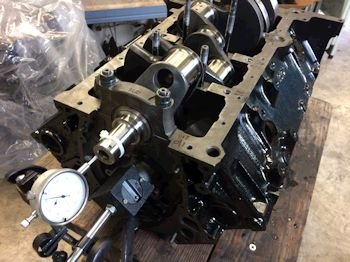
Crank is in temporarily so that I can check for piston to deck
height and if the block needs more clearance.
|
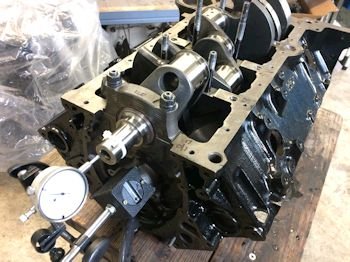
Right now thrust is at .005" but this is not final.
|
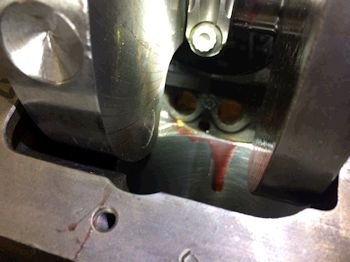
The rods do hit the inboard cam-side cylinder bottom. The
yellow marker is the general area that needs further clearancing.
|
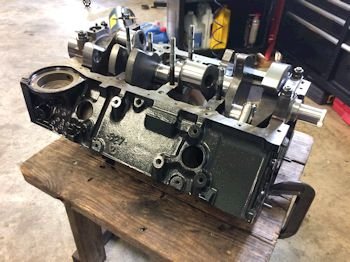
Next on the agenda is to gap the rings and clearance the block,
(the final cleaning of the block).
|
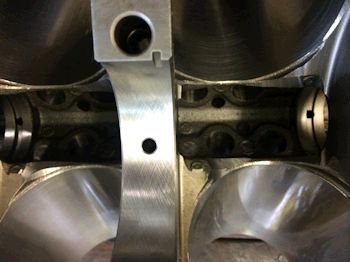
Bottom of cylinders, inboard near the cam-tunnel...that is the
area clearanced today...(then re-wash the block).
|
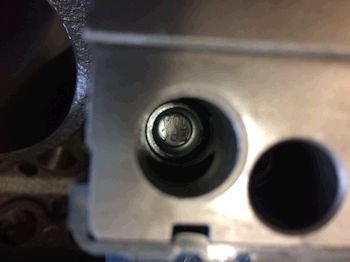
Rear main oil galley plug verification.
|
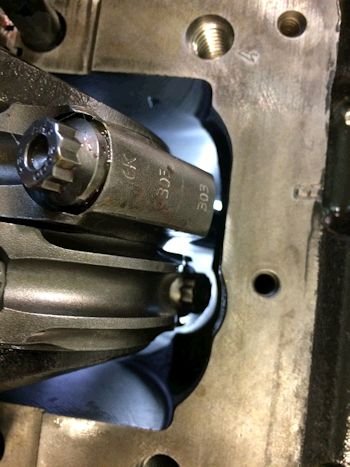
All rods/pistons installed and clearance checked. The rods
clear the inboard area after I spent 1 hour grinding and 1 hour
cleaning. This is the typical bolt-to-block clearance....about
.050"
|
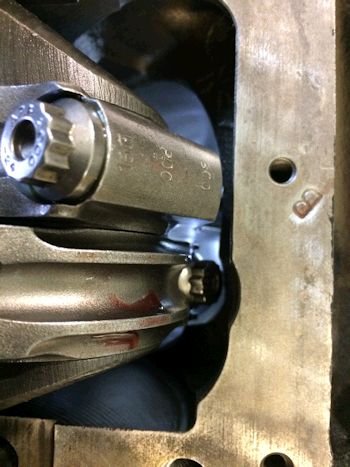
Here is the only area that needs a bit more clearance. This
is #2 piston/rod combo.
|
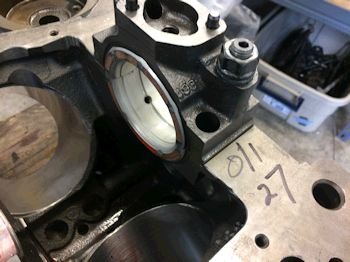
I had the rear main bearing clearance too tight, (after review of my
work). Now she's at .0027" with Clevite standard and
.001" mix.
|

The oil hole lines up pretty good.
|
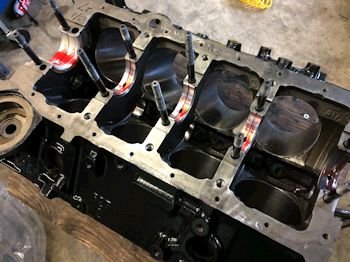
Camshaft bearings installed.
|
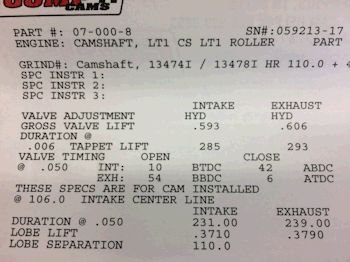
LE spec camshaft.
|
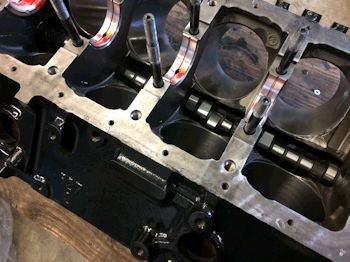
Camshaft installed.
|
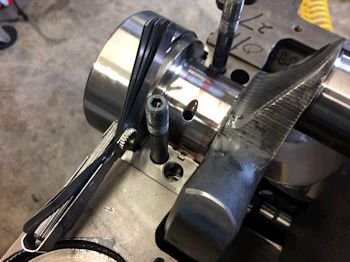
Crankshaft installed with rear main thrust check.
|
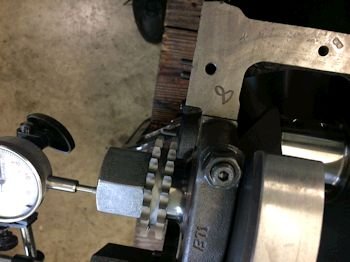
With the rear main cap torqued to spec. I measure .008"
crankshaft endplay.
|
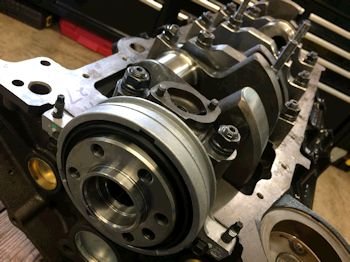
Brand new GM rear main seal housing.
|
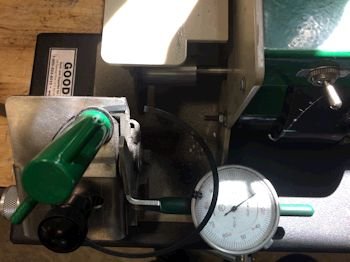
1mm rings gapped for all natural and occasional small nitrous
hit. .020" top and .018" 2nd ring.
|
|
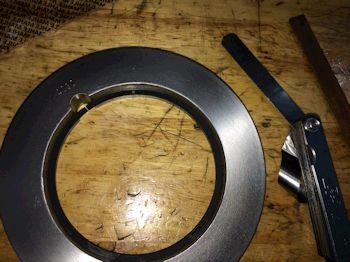
This is the top ring, 1mm, at .020" gap.
|
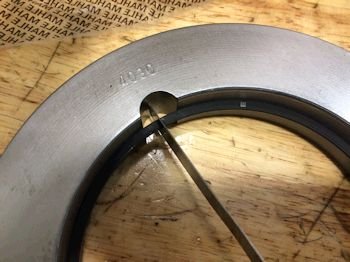
The 2nd ring at .018"
|
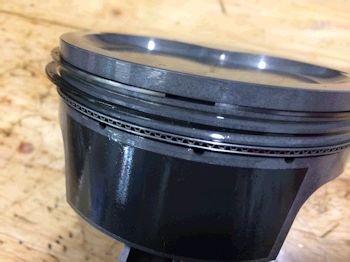
This is how the ring pack looks on the piston. The thin
rings conform to bore distortion and seal combustion gas better than
ever.
|
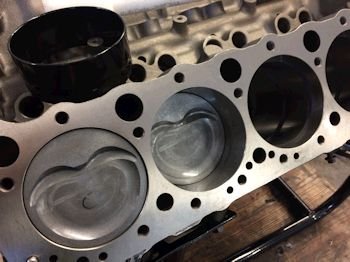
Pistons carefully installed and rotated on the crankshaft with the
cam timing gear installed to verify no interference between the rods
and the camshaft.
|
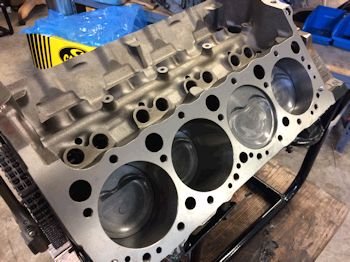
All good. No clearance problems. All pistons are at
.000" deck height.
|
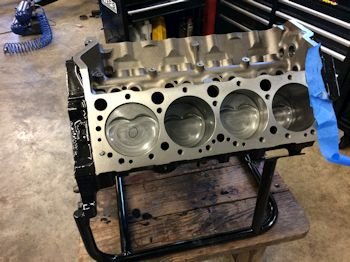
And some touch up painting.
|
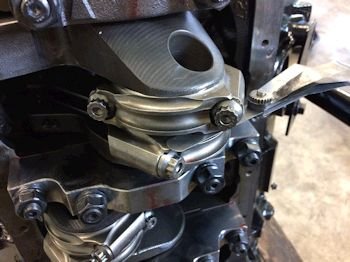
Callies rod bolts torqued to 75ft-lb with .020" feeler
inserted which is the rod side clearance.
|
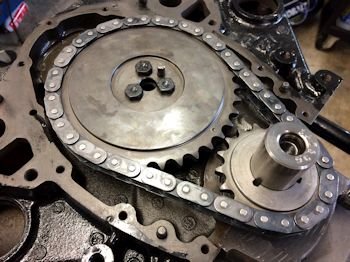
Cloyes extreme timing set.
|
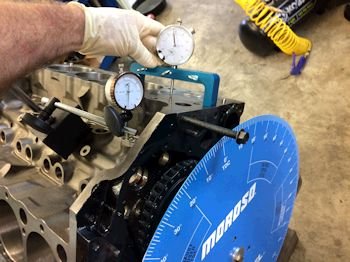
1st time using my new larger diameter degree wheel. Here I'm
finding TDC.
|
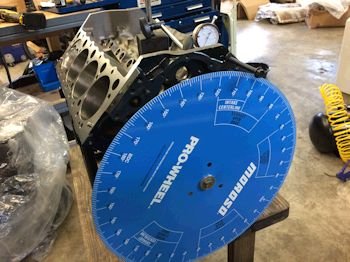
106 ICL exact. Crank sprocket at "0".
|
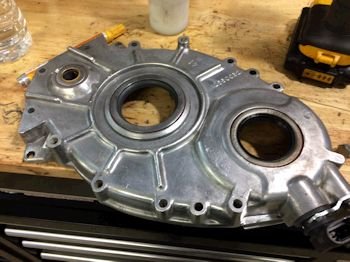
Cleaned up customer supplied timing cover.
|
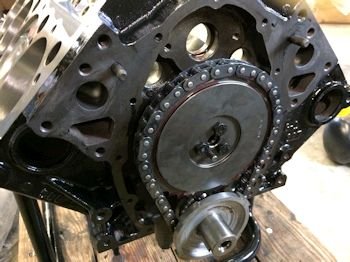
Used 1996 crank reluctor installed.
|
|
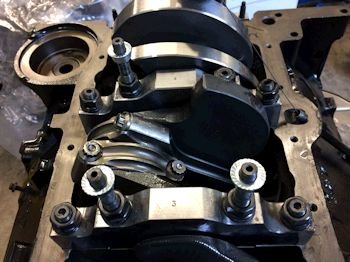
This photo is to show the oil level dip stick tube modification to
allow the stick to pass by the wide main cap.
|
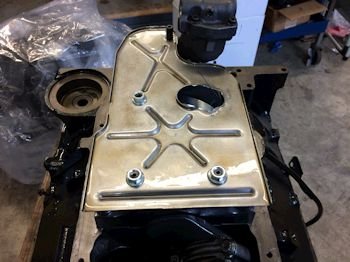
The stock windage tray gets trimmed.
|
|
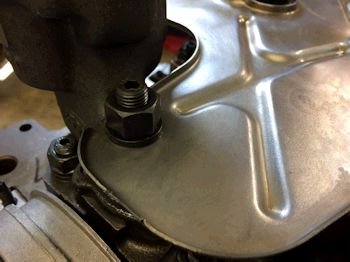
Melling 10552 oil pump installed via ARP stud.
|
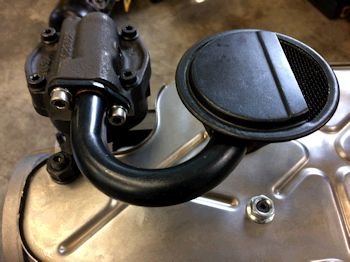
And Melling oil pump pickup.
|
|
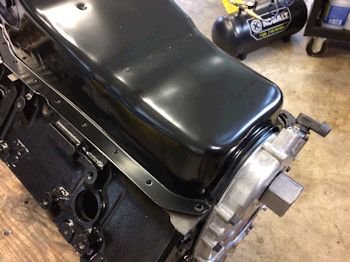
Oil pan test fit. The bottom front of the pan was hammered
so that the #1/#2 connecting rod bolts can clear.
|
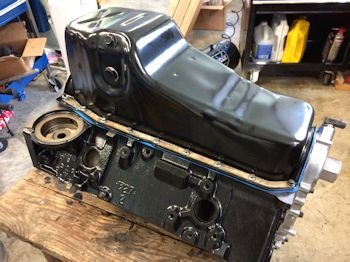
Pan installed.
|
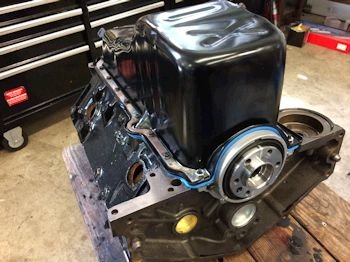
Photo view of the rear main seal housing...new from GMPP.
|
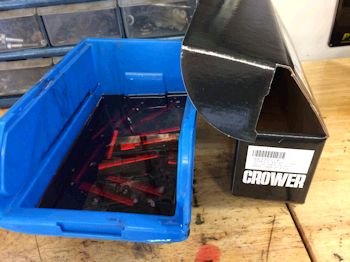
High quality stock style Crower lifters. They are soaking in
Amsoil 30W break-in oil. Yes it's red.
|
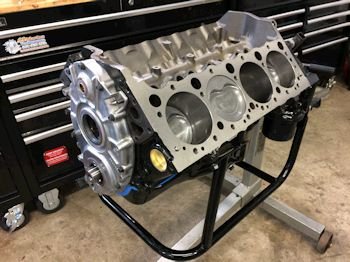
Engine now ready for cylinder heads.
|
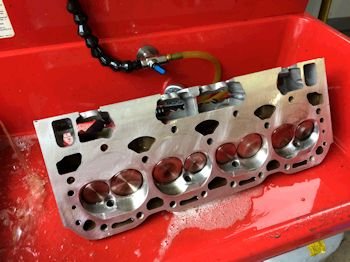
These are LE2 heads. I do nothing to them except to clean
them up in my parts washer.
|
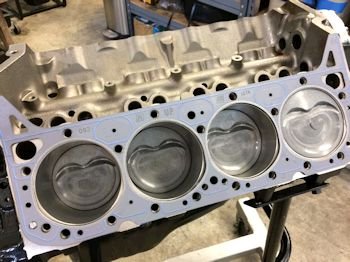
FelPro 1074 head gasket, (.039"). Pistons are
.000" in the hole. This will give 11.07 compression
ratio.
|
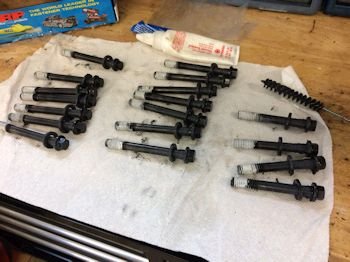
I spend quite a bit of time cleaning the ARP head bolts in the
parts washer and then adding sealant on the threads and lube on the
washer and under the head.
|
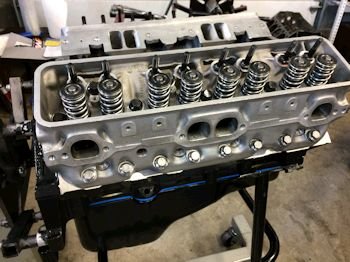
Head bolts torque @ 70ft-lb.
|
|
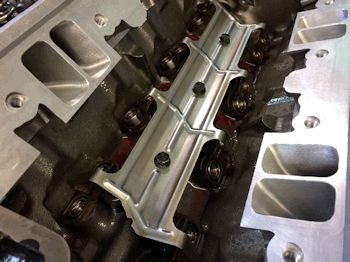
Lifter spider retainer and dog-bones all cleaned up and installed.
|
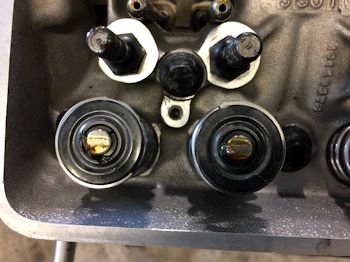
Stock 7.2" pushrods work well.
|
|
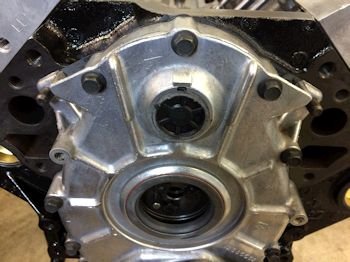
Holes getting filled in order to do the oil system pressure
test. Water pump drive plugged by plastic cap, (I have no more
Kennedy $1/2 pieces).
|
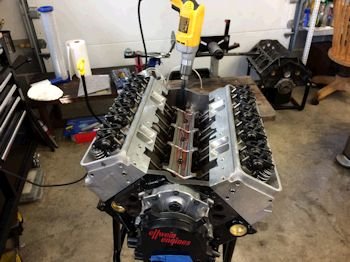
Borrowed optispark and Jeg's hub to keep the oil in.
|

Good pressure test and lifters all filled with oil well.
|
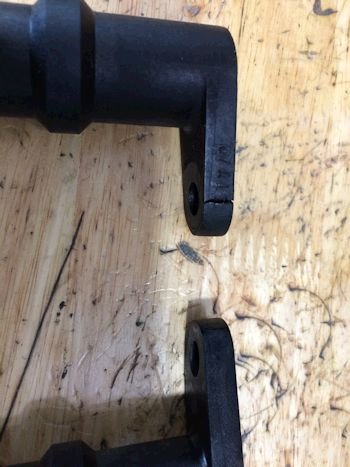
Oil pump drive gear gets changed out but I'll use a better core
for that. The one above is cracked. I found a good core in
my take-off drawer.
|
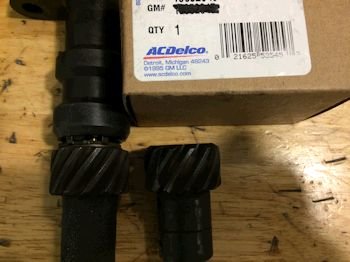
Replacing oil pump drive gear with new AC Delco gear.
|
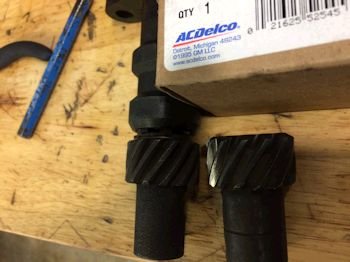
Here is another angle that shows the slightly worn gear that was
on the core.
|
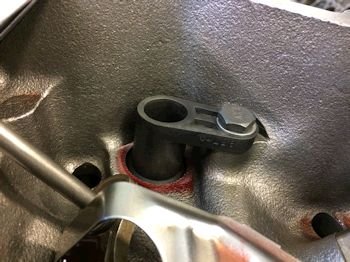
Gear installed. It cannot take more than 20ft-lb torque.
|
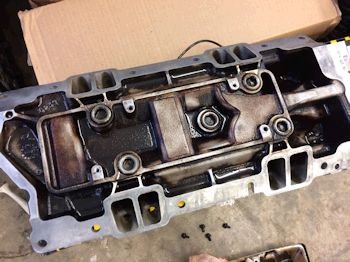
Cleaned up intake manifold. Not exactly pristine but all the
major gunk is cleaned away.
|
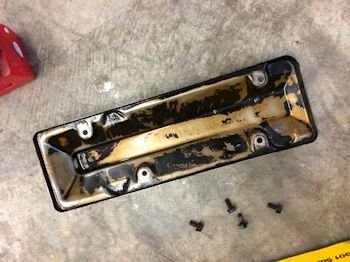
The tray inside was totally black.
|
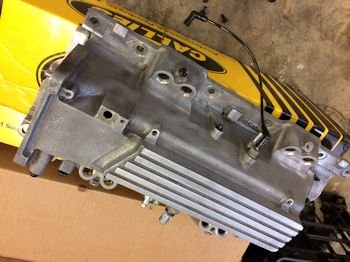
The outside of the manifold cleaned up very well.
|
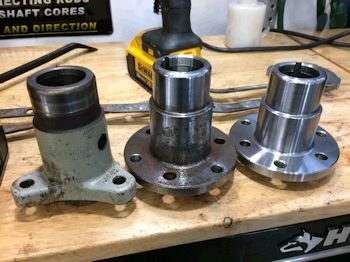
A variety of crankshaft hubs. Left is stock Bbody, middle is
Jeg's Bbody, right is Jeg's Fbody.
|
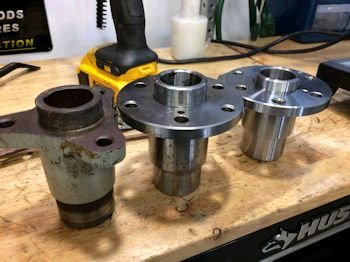
The Jeg's in the center came rusted like that new-in-box.
|
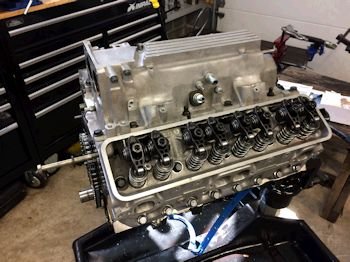
Intake manifold on and torque to 32 ft-lb
|
|
|
Stay tuned. The motor ships soon.
|
|
NOVEMBER 2017:
Engine is installed in the car and running well.
|